注塑模具作为现代制造业的核心装备,其结构精密性与复杂性远超其他模具类型,对操作规范性与维护保养水平提出了极高要求。科学合理的维护体系不仅能延长注塑模具的使用寿命,更能通过减少停机时间、降低不良品率直接提升企业经济效益。以下从设备选型、工艺优化、日常维护、故障预防到系统化管理,构建注塑模具全流程维护框架:
一、注塑模具设备选型的精准匹配
注塑机与模具的适配性是保障生产稳定性的基础。在设备选型阶段,需重点核查以下参数:最大注射量应覆盖制品重量的 120%-150%,避免因注塑机容量不足导致填充不完整;合模力需根据制品投影面积计算,公式为 F=PA(F 为合模力,P 为型腔压力,A 为投影面积),一般型腔压力取值 30-50MPa。同时需关注拉杆间距是否满足模具安装尺寸,模板行程是否匹配制品顶出高度。以汽车保险杠模具为例,若注塑机模板行程不足,可能导致制品脱模困难,损伤模具型芯。
工艺参数的优化同样关键。锁模力过大易导致模具分型面磨损,注射速度过快可能引发熔体破裂,模温过高则会加速模具钢材老化。建议采用 Moldflow 等模拟软件进行充填分析,确定最佳注射速度曲线与冷却水路布局。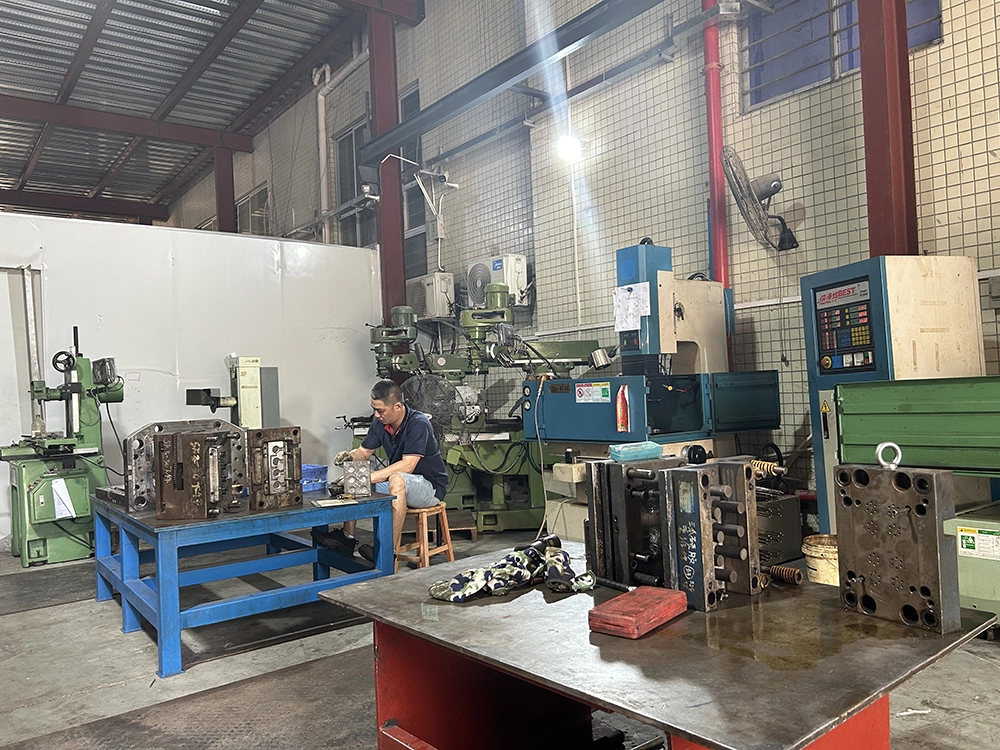
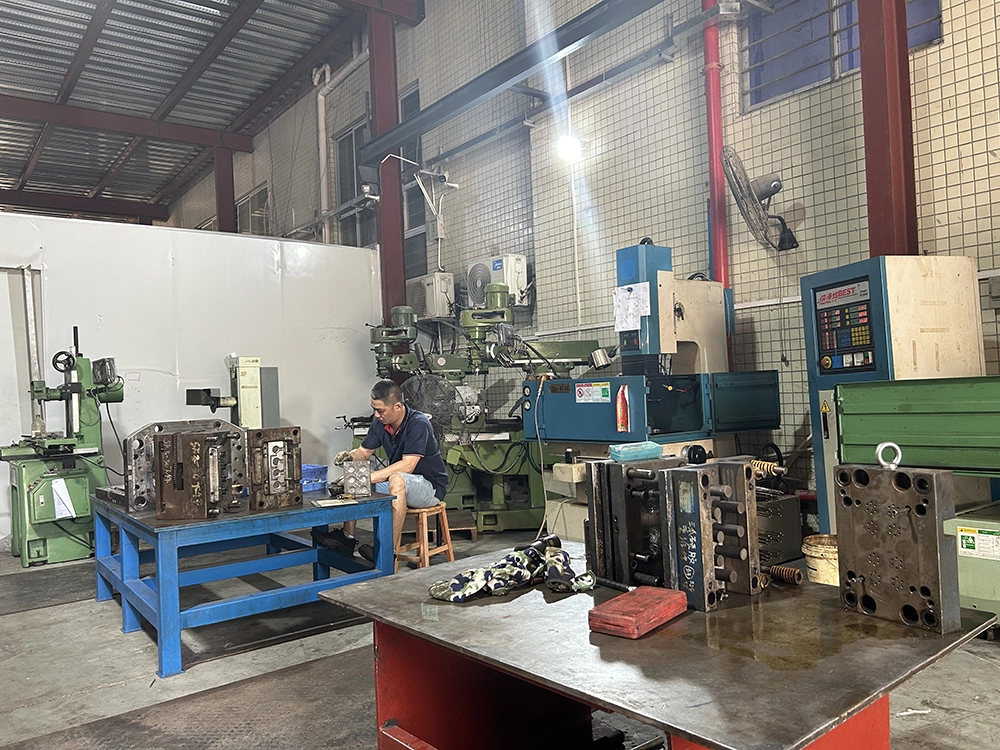
二、注塑模具日常维护的标准化作业
注塑模具的日常维护需建立标准化操作流程:
-
清洁与润滑
每次生产后需使用铜刷清理型腔、流道内的塑料残渣,严禁使用钢制工具以防划伤表面。导柱、顶针等滑动部件需每班加注二硫化钼高温润滑脂,夏季高温时段应增加至每日 2 次润滑,确保运动部件无卡滞。对于镜面模具,清洁时需使用无尘布蘸取专用镜面保护剂,避免指纹污染。 -
温度控制
模温机的冷却液温度应控制在 ±2℃波动范围内。冷却水道每季度需用 10% 草酸溶液循环清洗,硬水地区需缩短至每月一次,防止水垢沉积影响热交换效率。某医疗器械厂因冷却水道堵塞导致模具局部过热,制品收缩率波动超过 3%,经清洗后恢复稳定。 -
防锈处理
临时停机超过 24 小时时,需在型腔表面喷涂 WD-40 长效防锈剂,并用保鲜膜包裹隔绝湿气。长期存放的模具应垂直放置于防潮货架,关键部位加装保护套,环境湿度控制在 40% 以下。
三、注塑模具预防性维护的关键节点
-
定期深度保养
每周需检查顶出系统复位弹簧的弹性,每月拆解导柱导套测量磨损量,若间隙超过 0.05mm 必须更换。每季度对模仁进行磁粉探伤,检测隐性裂纹;使用扭力扳手校核锁模螺丝预紧力,确保符合设计要求。某汽车零部件厂通过季度探伤发现模仁裂纹,及时更换避免了批量性质量事故。 -
控制系统维护
热流道模具的加热元件需每生产周期用欧姆表检测阻值,偏差超过 5% 时立即更换。热电偶测温精度应定期校准,误差需控制在 ±1℃以内。液压抽芯系统停机后应排空油缸内液压油,防止密封圈老化漏油。 -
故障预警与处理
生产过程中若模具发出异常声响,或制品出现飞边、缩痕等缺陷,需立即停机检查。常见故障如浇口粘模可采用铜棒轻敲辅助脱模,严禁强行顶出导致模具损伤。导柱弯曲变形时,需成对更换导柱导套,避免单侧磨损加剧。
四、注塑模具全生命周期管理体系
-
档案化管理
每副注塑模具需建立电子履历卡,记录生产数量、维护记录、配件更换等信息。当生产数量达到设计寿命的 80% 时,需组织跨部门评估,判断是否需要更换模仁或增开备用模具。 -
智能监控系统
引入物联网传感器实时监测模具温度、压力等参数,通过机器学习算法预测潜在故障。例如,当冷却水路流量异常时,系统自动报警提示清洗或更换管道。 -
人员培训与交接
操作人员需通过专项培训,掌握模具装卸、参数设置等技能。交接班时需详细记录模具状态,包括已生产数量、异常情况及处理措施。
注塑模具的维护保养是一项系统性工程,从设备选型到退役管理的每个环节都需贯彻精细化理念。通过标准化操作、预防性维护与智能化管理,可将注塑模具的使用寿命提升 30%-50%,同时显著降低生产成本。企业应建立全员参与的维护体系,将模具维护纳入绩效考核,形成持续改进的良性循环,最终实现生产效率与产品质量的双提升。