在注塑加工中,模具费用往往占项目总投入的 60% 以上,甚至动辄数万元至数十万元。许多客户疑惑:“一个金属模具为何如此昂贵?” 事实上,
注塑模具的高成本源于其 “高精度、高复杂度、高可靠性” 的三重特性 —— 它不仅是塑料制品的 “模子”,更是融合材料科学、精密加工与工程经验的综合体。以下从六个维度解析注塑模具费用高的核心原因。
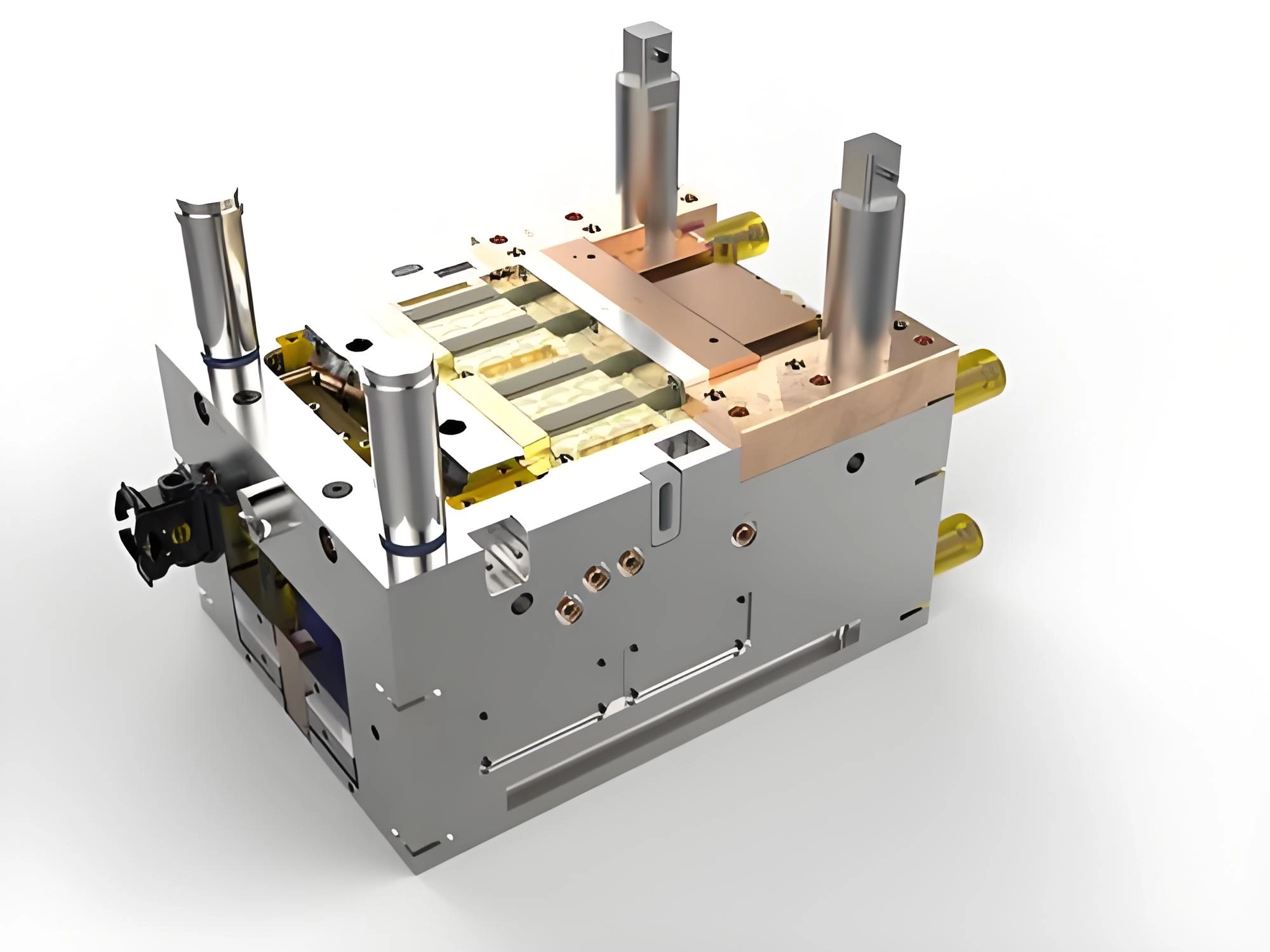
注塑模具的核心部件(模仁、型腔)需长期承受高温(200-300℃)、高压(80-150MPa)和塑料熔体的冲刷,对材料性能提出严苛要求:
- 基础材料昂贵:量产模具普遍采用进口合金钢材(如瑞典 S136、德国 718H),这类钢材纯度高(含碳量 0.3%-0.5%)、杂质少,能保证型腔表面光滑度(Ra≤0.8μm)和耐磨性(HRC50-55)。1 吨 S136 钢材价格约 5 万元,是普通碳钢的 5-8 倍。
- 热处理成本高:钢材需经过 “淬火 + 回火” 多道热处理,将硬度从初始的 HRC20 提升至 HRC50 以上,同时消除内应力。仅热处理工序,每吨钢材成本就增加 8000-12000 元。
- 辅助材料不便宜:模具配件(如导柱、顶针)需用轴承钢(SUJ2),热流道系统采用铜合金(铍铜)增强导热性,这些特种材料进一步推高成本。
注塑模具型腔的尺寸精度直接决定塑件质量,哪怕 0.01mm 的误差都可能导致产品飞边或装配不良。这种高精度要求对加工设备和工艺提出极致挑战:
- 高端设备是标配:型腔加工需依赖五轴 CNC 加工中心(单价 200-500 万元),实现三维曲面的微米级切削(精度 ±0.005mm);复杂结构(如深腔、窄缝)需用慢走丝电火花机床(单价 100-300 万元),切割精度达 ±0.002mm。
- 加工周期长:一个中等复杂度的手机壳模具(单腔),从粗加工到精加工需 20-30 道工序,累计加工时间超 100 小时。若采用多腔设计(如 8 腔),加工时间翻倍,且对设备稳定性要求更高(避免腔与腔之间的误差)。
- 人工成本占比高:操作高端设备的技师需 5 年以上经验,月薪普遍在 1.5-3 万元;每道工序后需用三坐标测量仪(精度 ±0.001mm)检测,单次检测耗时 1-2 小时,人工与设备折旧成本显著。
注塑模具设计绝非简单 “复制产品形状”,而是需平衡 “成型可行性、生产效率与成本” 的系统工程,复杂产品的模具设计成本占总费用的 15%-20%:
- 功能模块设计:除型腔外,需设计浇口(控制熔体流动)、冷却系统(保证塑件均匀冷却)、排气槽(避免困气)、脱模机构(顶针 / 滑块)等。以汽车保险杠模具为例,仅冷却水路就需布置 30-50 条,确保壁厚 3mm 的塑件冷却时间控制在 30 秒内。
- 模流分析不可少:通过 Moldflow 等软件模拟熔体流动,预判缩痕、熔接痕等缺陷,优化型腔结构。一次完整的模流分析需 2-3 天,资深分析师日薪超 1000 元。
- 定制化适配:带倒扣的产品需设计滑块机构(增加 20%-30% 成本);薄壁件(如 0.5mm 的电子外壳)需用热流道系统(单套热流道成本 2-5 万元),避免熔体提前凝固。
模具制造完成后,需经过 2-5 次试模才能达标,每次试模成本从数千元到数万元不等:
- 试模耗材:每次试模需消耗 5-20kg 原料(如 PC 料单价 40 元 /kg),加上注塑机能耗(每小时电费 50-100 元),单次试模直接成本超 2000 元。
- 修模成本高:试模后若出现飞边(模具间隙过大)、缩痕(保压不足)等问题,需重新打磨型腔(0.01mm 级精度)、调整顶针位置或修改流道,每次修模耗时 1-3 天,人工成本增加 5000-1 万元。
- 时间成本隐性损耗:试模与修模周期通常占模具总周期的 30%,若因模具延期导致客户量产计划推迟,供应商可能面临违约金,倒逼工厂投入更多资源加速修正,间接推高成本。
客户对模具的使用寿命要求(通常 5 万 – 100 万模次)直接影响材料与工艺选择,寿命越长,初期投入越高:
- 耐磨性升级:要求 100 万模次的模具(如矿泉水瓶盖),模仁需用 H13 钢材(淬火后 HRC55-58),并进行氮化处理(表面硬度提升至 HV1000),成本比普通模具高 30%-50%。
- 结构强化:多腔模具(如 32 腔针管模具)需增加模架厚度(从 30mm 增至 50mm),采用高强度导柱(直径 20mm 以上),避免长期生产导致的变形。
- 易损件冗余设计:顶针、弹簧等易损件采用进口品牌(如日本米思米),虽单价是国产件的 3-5 倍,但使用寿命提升 10 倍,减少后期停机更换成本。
与标准化零件不同,模具是 “一对一” 定制产品,无法通过批量生产摊薄成本:
- 无复用性:手机壳模具无法用于生产水杯,哪怕同类产品,尺寸差异 0.5mm 就需重新开模。小批量订单(如 5000 件)的模具成本无法分摊,导致单件塑件的模具摊销费用高。
- 小批量溢价:年产量 1000 件的精密零件,模具可能仅需生产 1000 模次,但制造标准与量产模具一致(否则易出故障),供应商需通过提高单价覆盖固定成本。
注塑模具的高费用本质是 “高精度制造 + 长期可靠性” 的必然结果:优质模具虽初期投入高,但能保证塑件合格率(从 80% 提升至 99.5%)、缩短成型周期(从 60 秒降至 30 秒)、延长使用寿命(减少重复开模),最终降低整体生产成本。
对客户而言,选择模具时需避免 “只看价格”:低价模具可能采用劣质钢材(如 45# 钢替代 S136),导致生产 1 万模次后型腔磨损,塑件尺寸超差;而合理价格的模具,往往能在 3-5 万模次内收回成本,成为长期生产的 “盈利工具”。